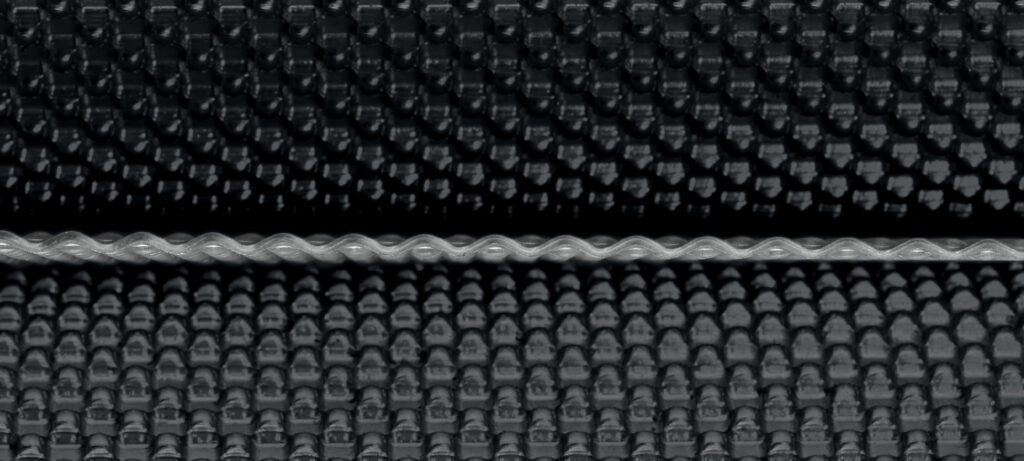
Hadley Group’s internationally patented UltraSTEEL® process is a cold rollforming technology that enables you to improve product efficiency, save weight and reduce the use of raw materials.
Fully patented and exclusive to Hadley
Create stronger metal parts
Produce metal profiles up to 20% stronger with our patented UltraSTEEL® roll-forming process.
Use less material
Cut the weight of your cold-rolled metal parts by up to 20% — without sacrificing strength or stability.
Reduce your environmental impact
Create thinner and lighter finished products to minimise your use of raw materials and the fuel used in transport.
How does it work?
UltraSTEEL® is a patented cold-rolling metal process that can be included as a part of your fully automated production line.
By passing metal sheets through a pair of textured rollers, the roll-formed metal gains a uniform dimpled effect.
This dimpled effect improves the strength of your finished metal parts — helping you to use less metal and reduce your impact on the environment.
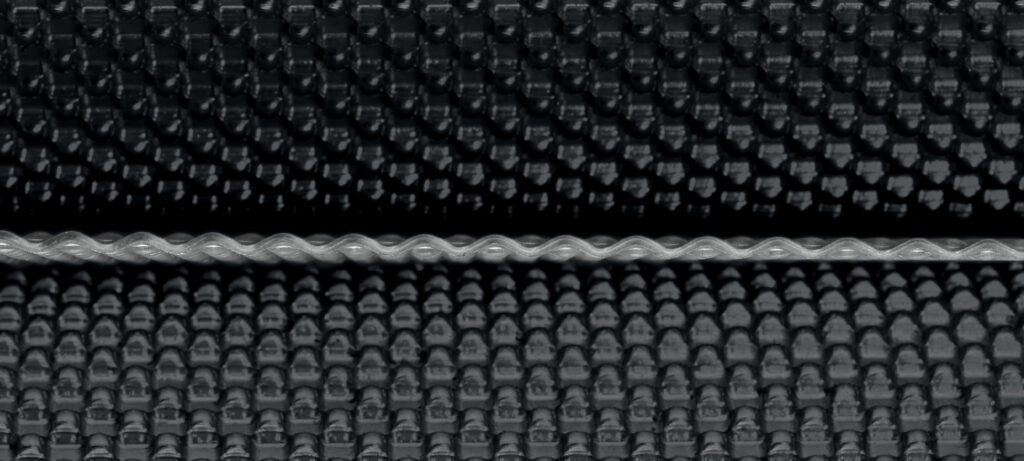
Introduced in 1982 and awarded the Queen’s Award for Enterprise: Innovation in both 2006 and 2014, it continues to shape the use of cold rolled metals across a huge range of applications.
- The result of more than 35 years’ R&D investment
- Up to 20% more strength, up to 20% less raw material
- Over 1 billion metres produced each year
- Over 100,000 tonnes produced each year
- Manufactured on over 300 rolling machines worldwide
STRONGER BY DESIGN
UltraSTEEL® is a cold rolled pre-forming process with a dimpled metal structure that creates a locally work-hardened base metal. It is the metal formed between the two mating rolls which produces this dimpled pattern across the surface of the material. The effective thickness of the material is increased by locally deforming the strip to twice its original gauge, resulting in substantial work-hardening and increased strength.
GREENER BY DESIGN
UltraSTEEL® products use less metal, reducing the impact your business has on the environment. It also results in products that are lighter, enabling more efficient shipping and reduced transport related pollution. These benefits are further enhanced by efficient product designs, high accuracy manufacturing capabilities and the ability to apply the UltraSTEEL® process to recycled metal.
VIRTUAL SIMULATION
Your project will benefit from our support services – including the use of sophisticated simulation software to assess the benefits of UltraSTEEL® in relation to any rolled product.
The UltraSTEEL® process:
- STEP 1: A simulation is specified using your material properties and metal thickness.
- STEP 2: Forming of the rolled product is simulated to determine the stress and strain distribution within the metal.
- STEP 3: Your product is then virtually tested in an arrangement or system that reflects the application.
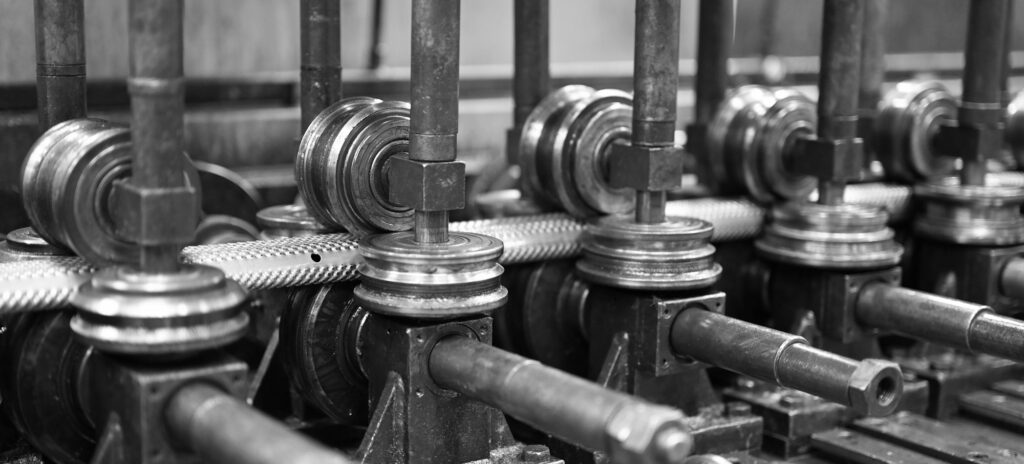
See the benefits before production
Our expert engineers use simulation technology to model the effects of UltraSTEEL® on your specific metal parts.
Using the latest software to carry out virtual tests, we can simulate your specific materials and designs — to show you exactly how much our exclusive process can improve the strength of your parts.