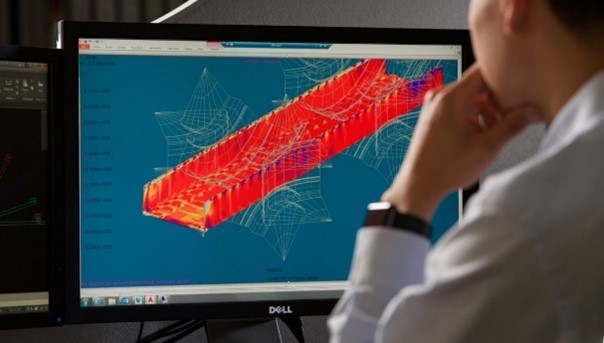
Predict and Prevent with Simulation Technology
Save time on product development
Reach an optimised design for your parts and tooling faster — with advanced computer simulations to model the behaviour of your roll-formed products.
Reduce the cost of production trials
Save time and materials by avoiding the trial and error of repeated prototypes — while reducing your environmental impact.
Spot problems before they happen
Prevent issues and defects at an early stage by combining simulation technology with the expertise of our experienced engineers.
Over the last 10 years Hadley Group have invested in one of the most technically advanced cold roll forming design and production engineering operations of its kind, ensuring maximum productivity and efficiency at every stage of your project.
- Finite Element Analysis (FEA)
- CAD Simulation Tools
- Non-linear Software
- Simulation to BSEN Standards
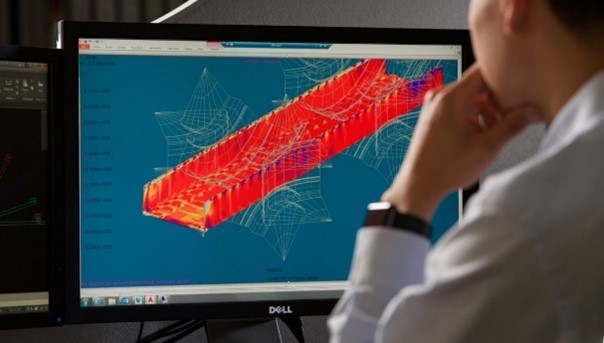
Speak to our Custom Roll Forming experts today
Our in-house team of specialist engineers have helped countless companies in a range of sectors to predict, prevent, and optimise their designs.
So if you’ve got a complex product that can put our simulation technology to the test, we’d love to hear about it.
Utilise these capabilities in your project development to:
- Quick evaluation of the performance in new products and systems
- Optimisation of tooling design to minimise forming defects
- Reduction in the cost and lead time of new tooling
- Ability to support our customer with their own product development
- Optimisation in the design of machinery assets
- Capability to continuously update design principles
We recognise that validation of simulation data is key to this technology.
For this reason, HGT regularly combine simulation technology with physical testing to ensure the results we simulate match reality as closely as possible.
Examples of analysis carried out using this technology include:
- Complex geometry product bending (3 and 4 point)
- Global and localised buckling (under compression)
- Acoustic behaviour of rolled products within a system
- Screw and bolt slot pull-through
- Product cutting (shear and crop cutting)
- Full system simulation to BSEN testing standards
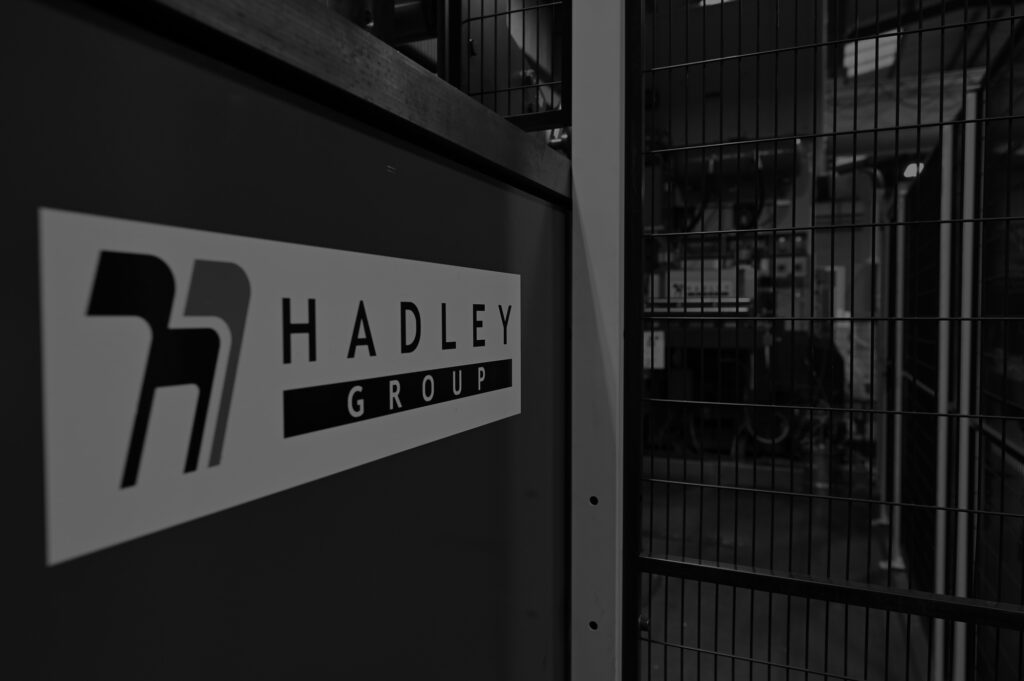