What can you do with cold roll forming?
- Profiles with a thickness of 0.3 to 8 mm and a width of up to 1.3 m;
- Wide range of geometrical possibilities;
- Very narrow tolerances, from ± 0.05 mm;
- Suitable for ferrous, non-ferrous, stainless steel and other deformable metals;
- Ability to form materials with polished and pre-painted surfaces;
- In-line machining such as punching, cutting, bending and trimming to length;
- Ability to form closed shapes by in-line welding.
Contact us
Want to know what is possible with cold rolling? As a specialist, we would be happy to discuss your specific requirements for cold rolled profiles with you at an early stage. Together with you, we will find the best solution. This often leads to new insights and savings in time and costs.
- It is ideal for constant profile parts with long lengths and large volumes;
- Ensures a high degree of consistency and accuracy;
- Is suitable for a wide range of metals, such as stainless steel, aluminium and prepainted steel;
- Enables customised product design and production;
- Provides effective solutions to complex challenges;
- Is environmentally friendly.
The cold rolling process
The cold rolling process consists of a constant bending operation in which a long strip of coiled metal (usually steel) is passed through a series of pre-formed rolls that gradually shape the metal to achieve the desired cross-sectional profile.
Cold roll forming offers a number of advantages over extrusion. The roll forming process is faster and uses less energy than extrusion. It also offers significant weight savings and increased strength (as the metal is hardened in the cold state).
One of our greatest strengths is our ability to translate complex customer requirements into practice. Cold rolled steel has several advantages that can be very interesting for different sectors, such as: automotive, construction, industry and agriculture.
Collaboration for complex metal profiles
Your project requirements are assessed by our team of 50 full-time engineers and technicians within Hadley Group Technology. They will work as an extension of your in-house designers to translate your complex requirements into highly effective, quality solutions.
As specialists in research and product development, design, manufacturing, and technical support for tooling and machinery, we use the latest developments in computer simulation technology, advanced engineering hardware, and the expertise of our in-house team.
Hadley Group Technology
Think with us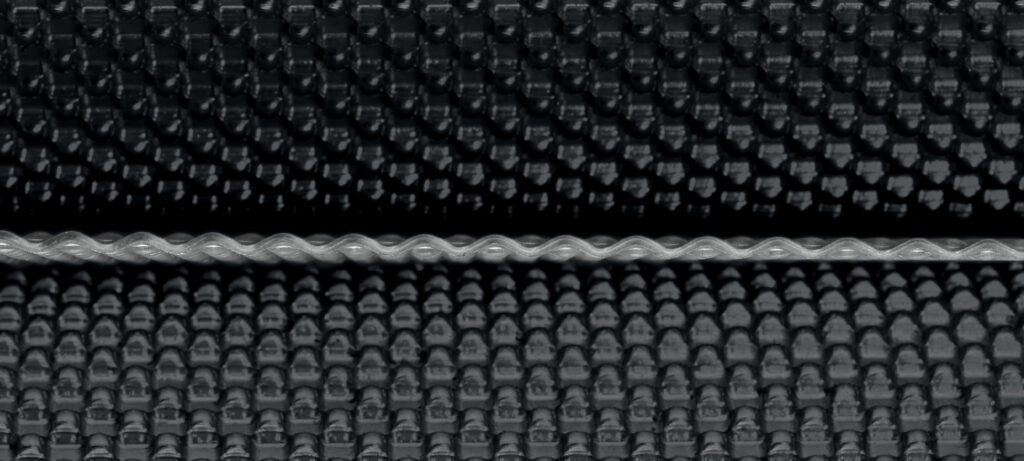
UltraSTEEL®
The UltraSTEEL® process is a pre-machining technology for the base material. UltraSTEEL® has helped customers from various industries around the world to improve product efficiency and product strength while reducing weight and use of raw materials.